Thanks to its capacity to monitor the very core of materials, the Sensity Tech technology can meet the heightened demands of the predictive maintenance, non-destructive testing and scalable HMI sectors. It quickly provides the required data required to preserve product quality over time, it guarantees structural health, anticipates failure, enhances performance and extends service life, while generating feedback in response to mechanical stimulations.
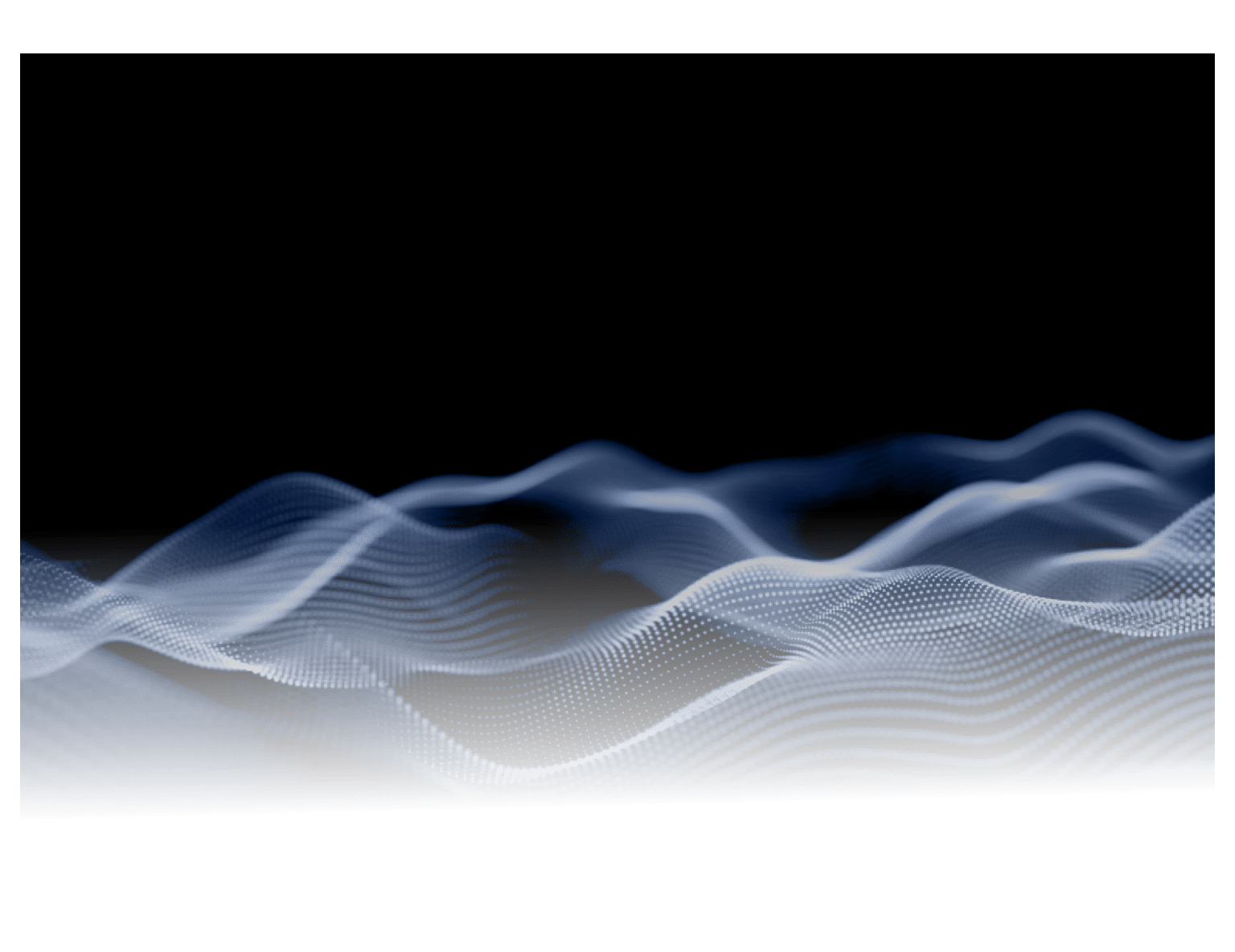
A three-tiered intervention
Test bench instrumentation
Material and parts analysis (impact, bending, compression tests, etc.) in order to provide additional information to the sensing systems that are being used. Occasionally used by materials divisions or design offices for the development of parts, to verify mechanical resistance or to gain knowledge on materials.
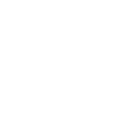
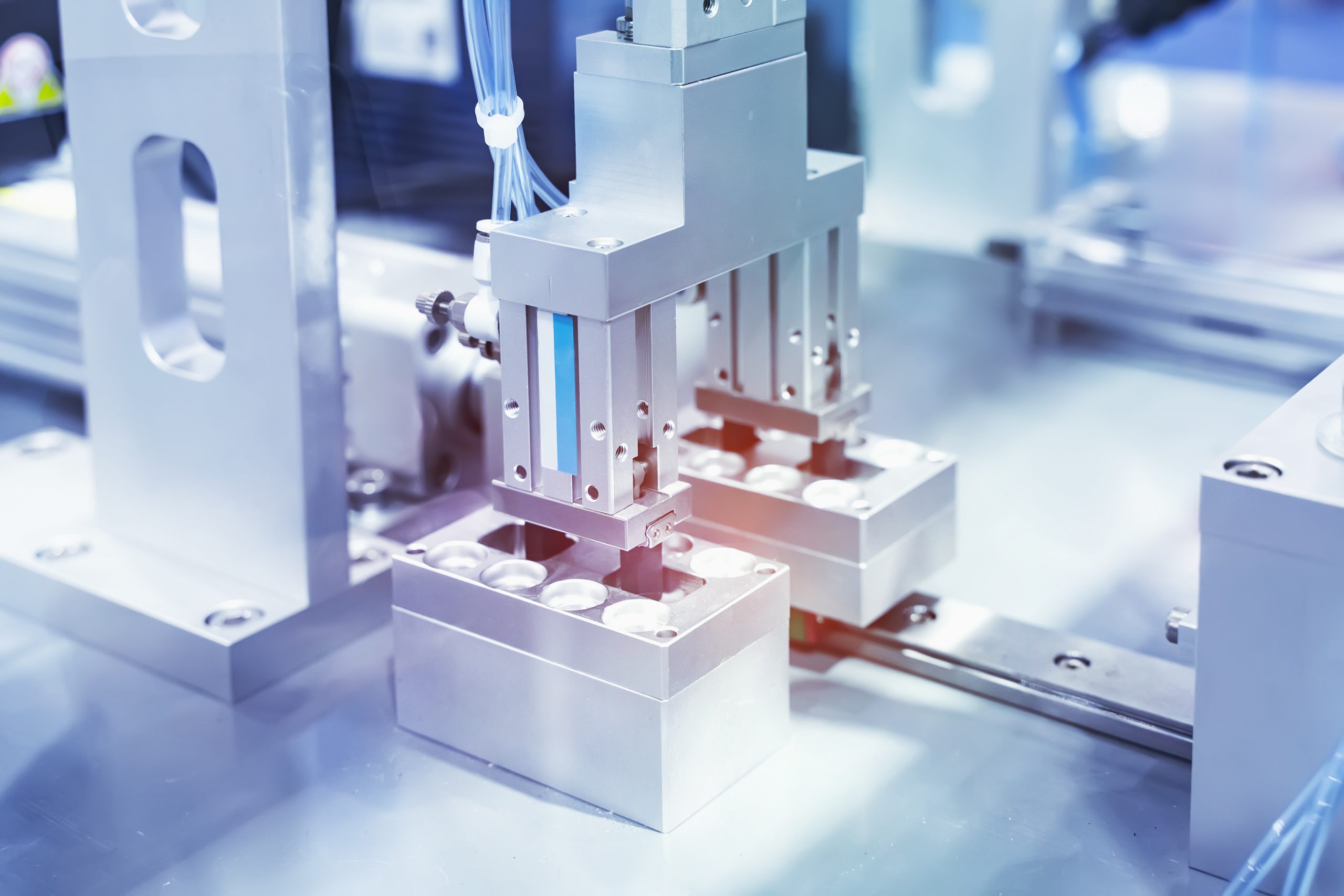
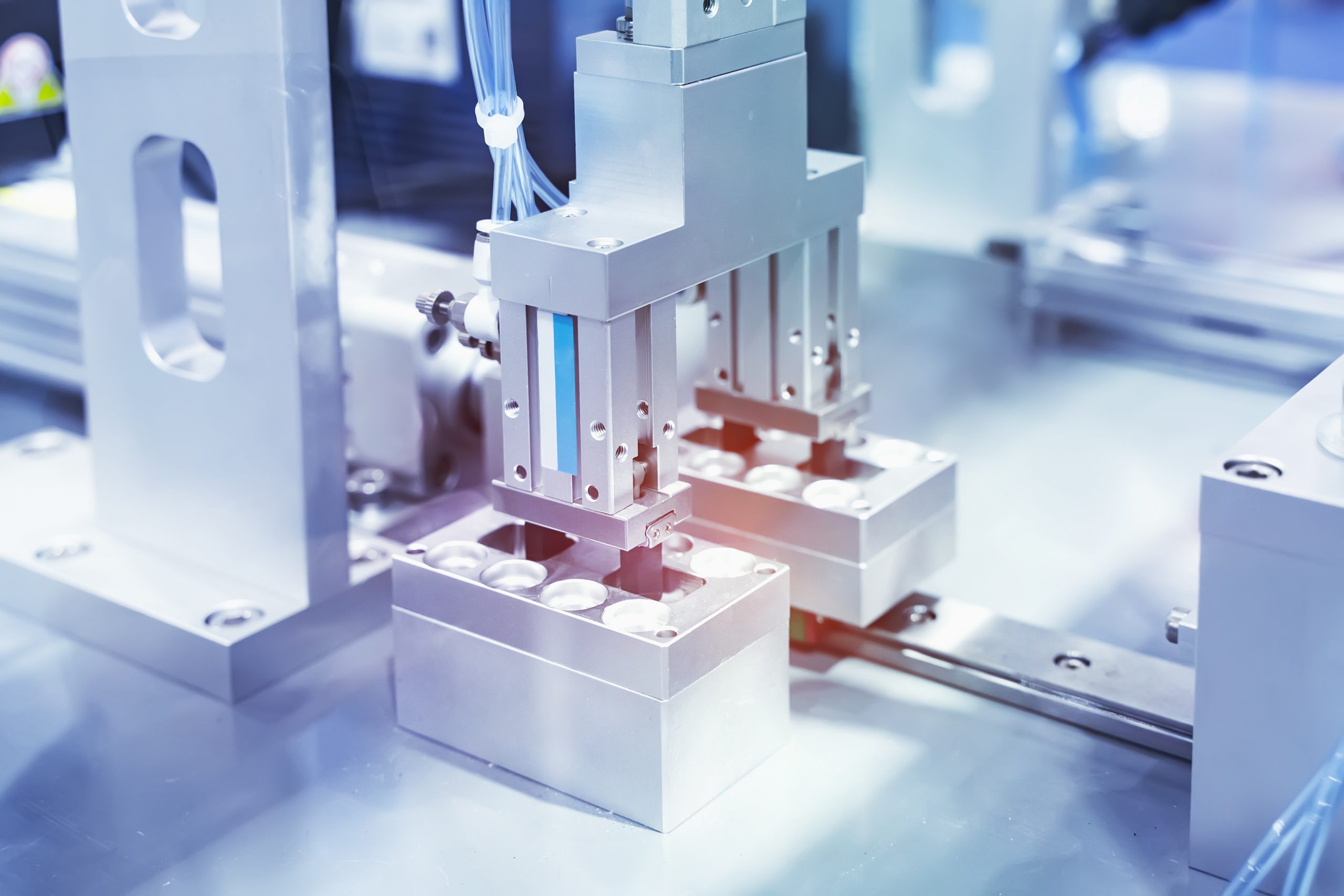
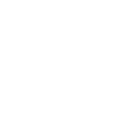
Test bench instrumentation
Material and parts analysis (impact, bending, compression tests, etc.) in order to provide additional information to the sensing systems that are being used. Occasionally used by materials divisions or design offices for the development of parts, to verify mechanical resistance or to gain knowledge on materials.
Non-destructive testing on production lines
Automated test bench that allows for non-destructive testing on a series of parts with the use of Sensity Tech. Assess quality and identify the various manufacturing defects.
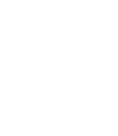
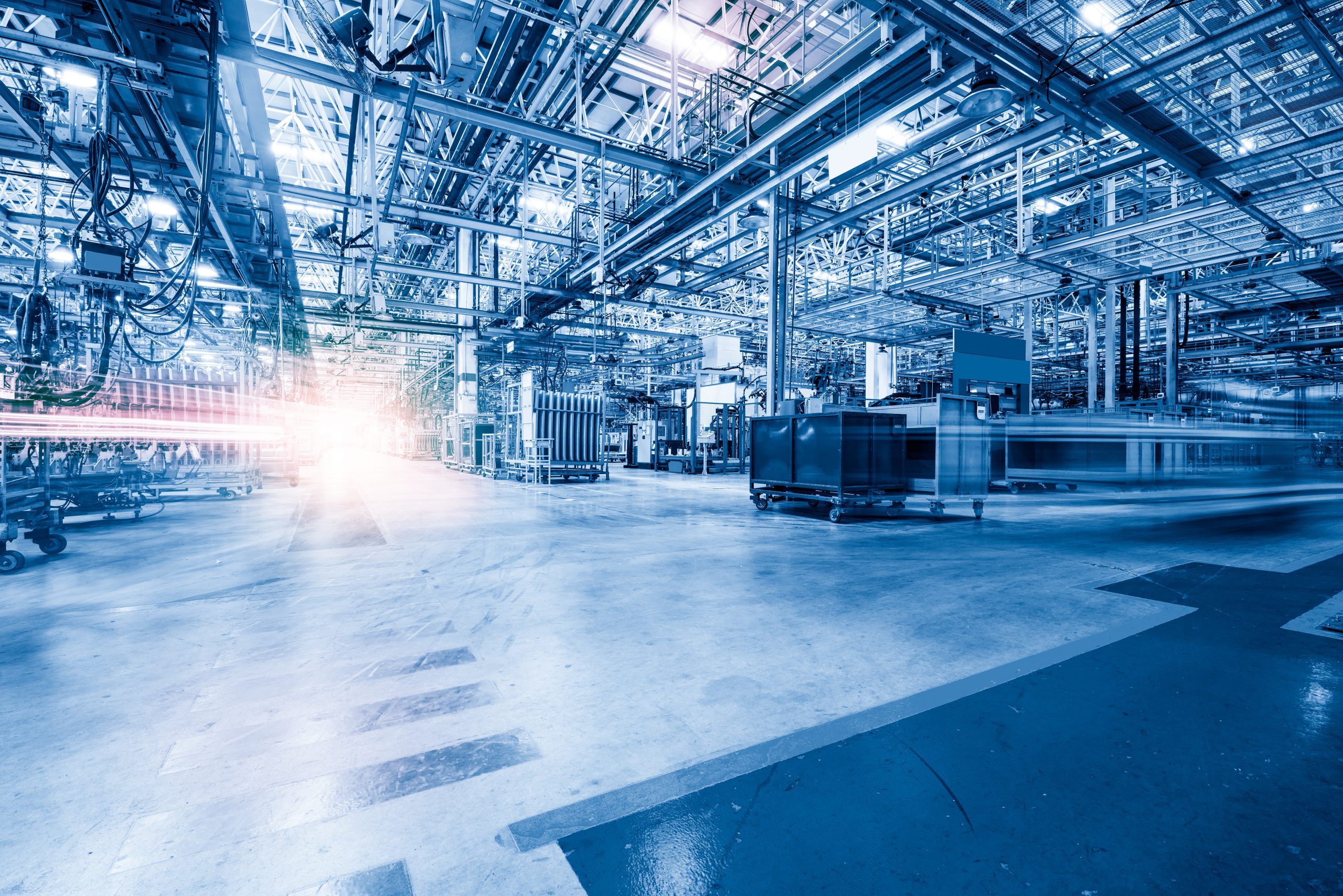
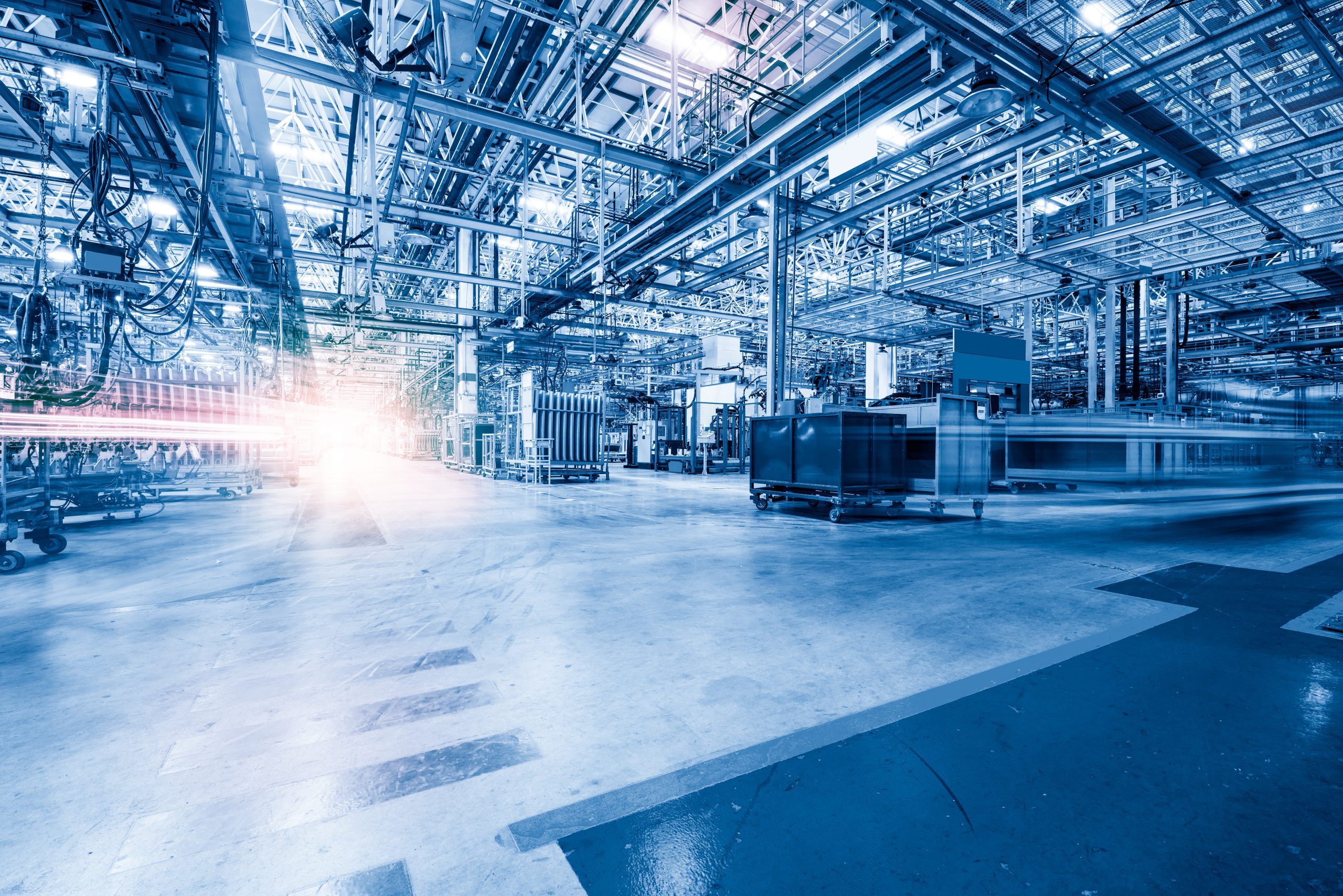
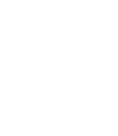
Non-destructive testing on production lines
Automated test bench that allows for non-destructive testing on a series of parts with the use of Sensity Tech. Assess quality and identify the various manufacturing defects.
Predictive maintenance on running systems
- Monitoring with a non-integrated solution that will be connected to the device after each use, in order to perform a “scan” and identify damaged areas, thereby reducing maintenance time.
- Real-time monitoring with a system integrated to the device to identify deformed, damaged or impacted areas at different levels of accuracy and over time.
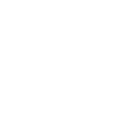
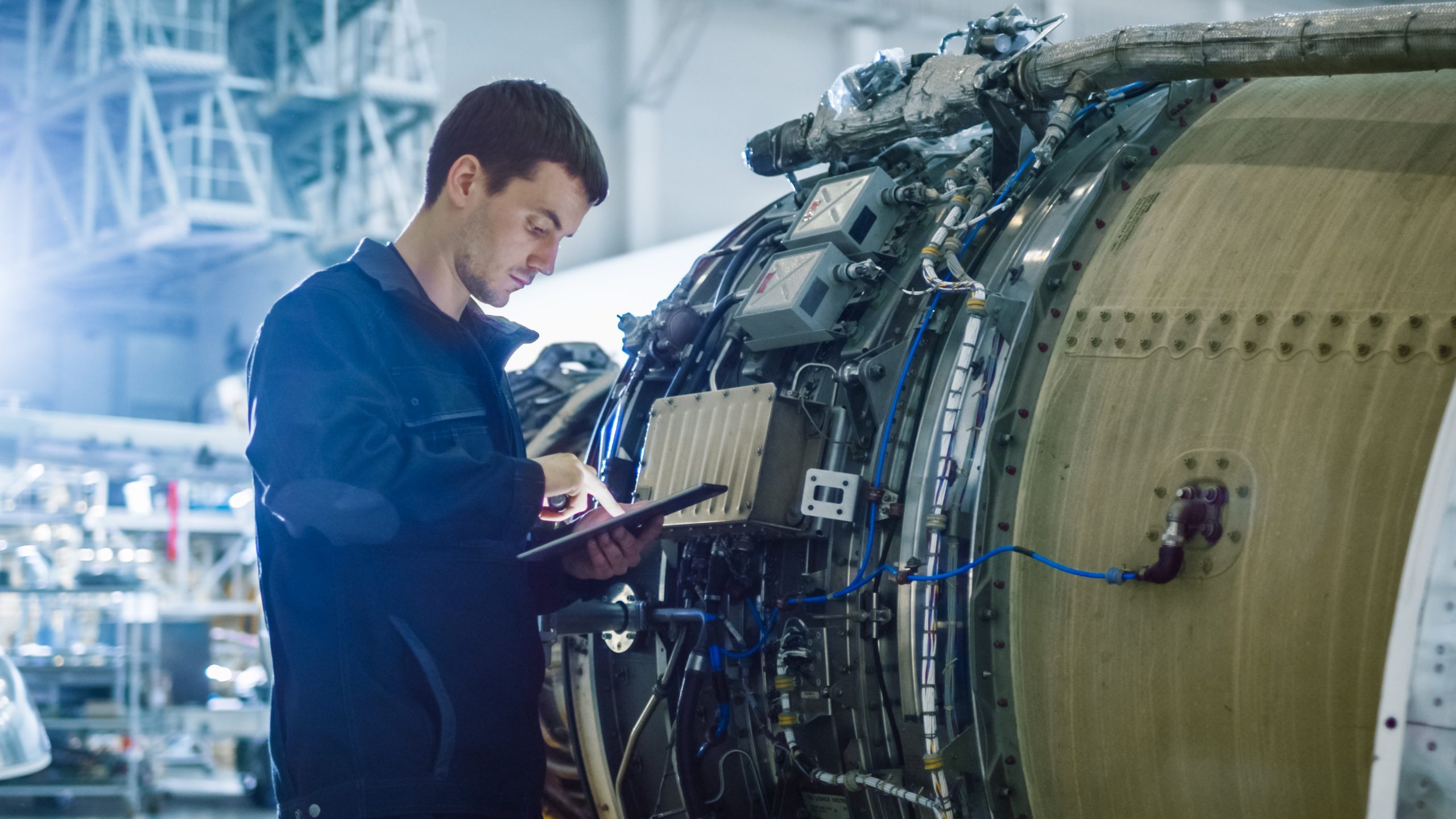
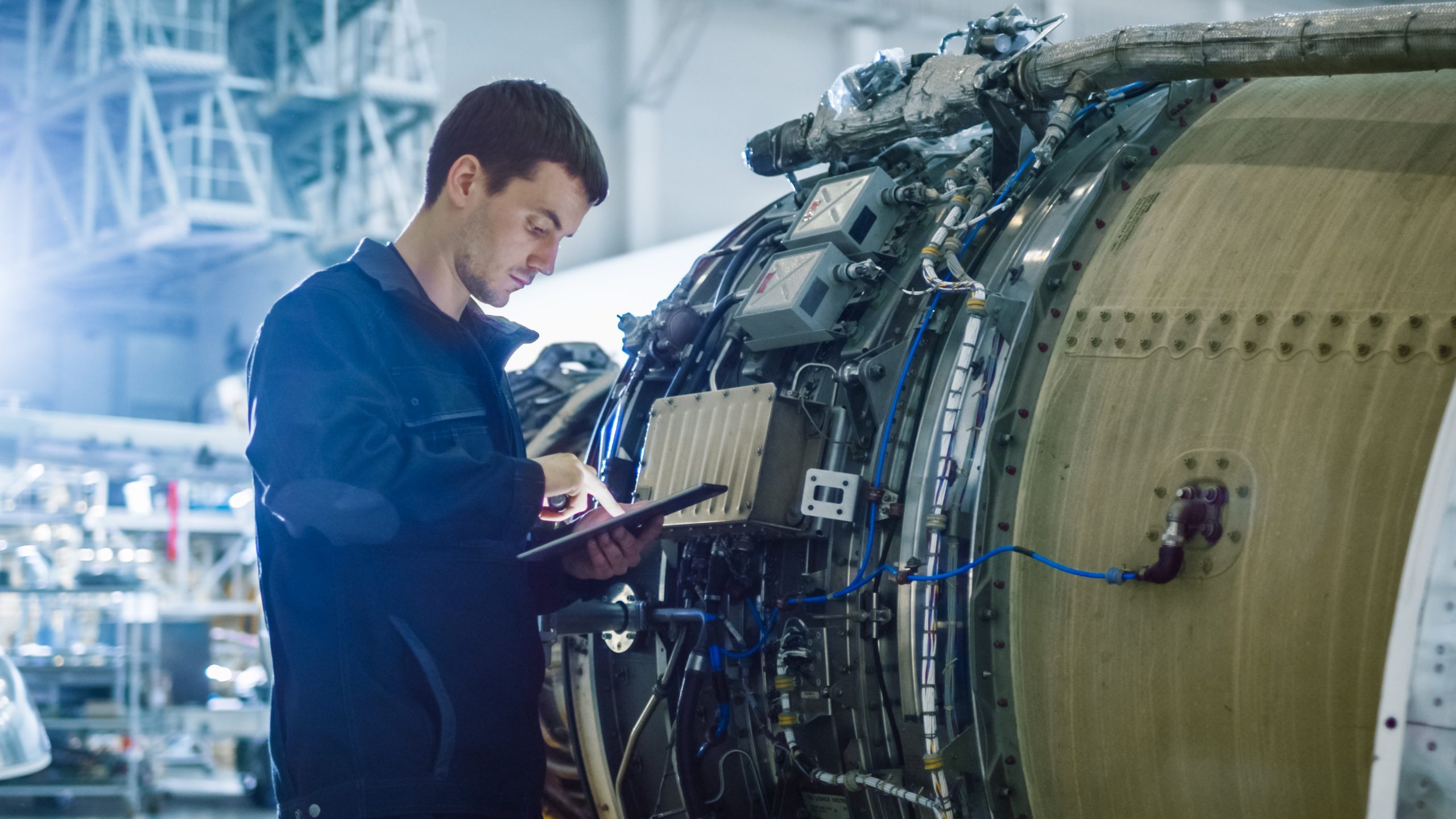
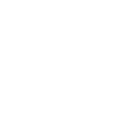
Predictive maintenance on running systems
- Monitoring with a non-integrated solution that will be connected to the device after each use, in order to perform a “scan” and identify damaged areas, thereby reducing maintenance time.
- Real-time monitoring with a system integrated to the device to identify deformed, damaged or impacted areas at different levels of accuracy and over time.
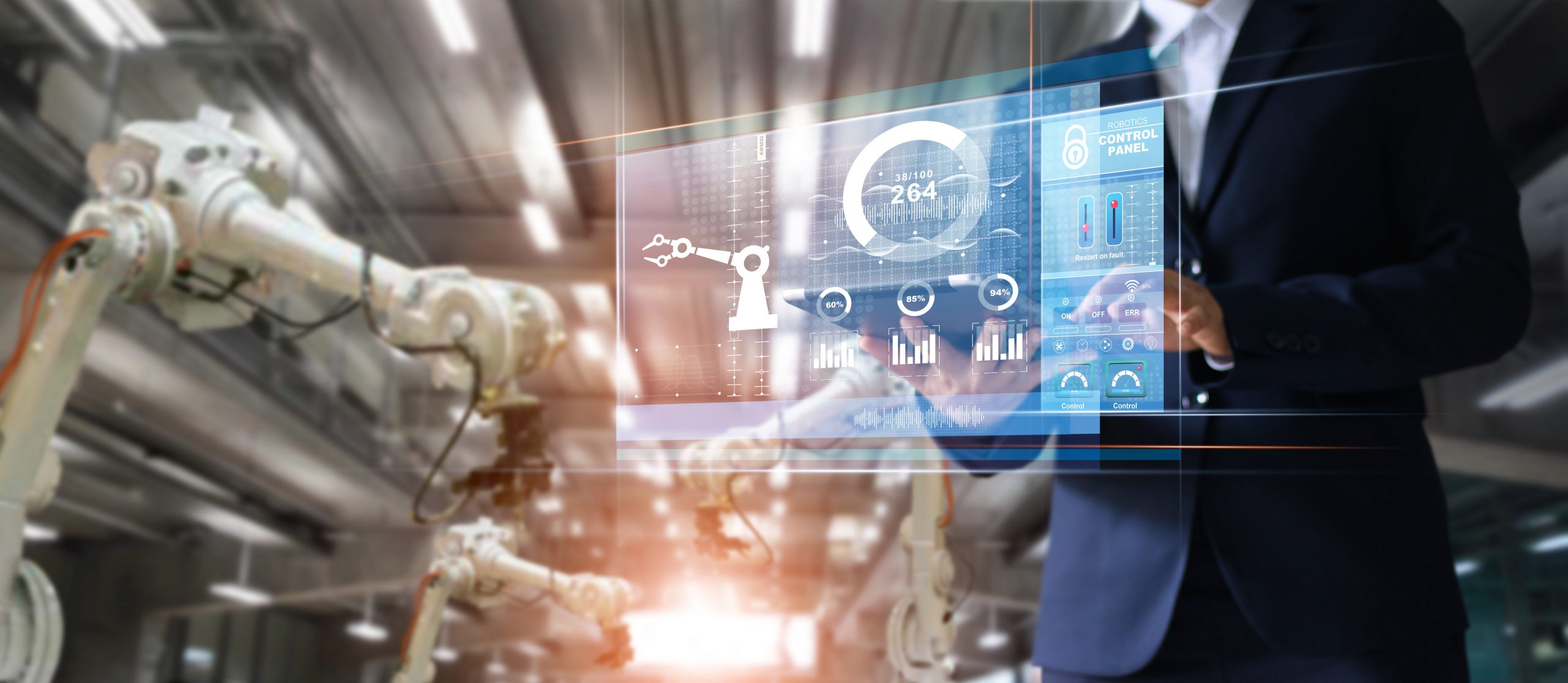
Scalable HMIs
Adaptation of materials with surfaces that are sensitive to pressure and deformation in order to set up feedback and thus control systems remotely.
Its HMIs are scalable, adaptable to all surfaces, multi-touch, etc. – Each material can become an HMI!
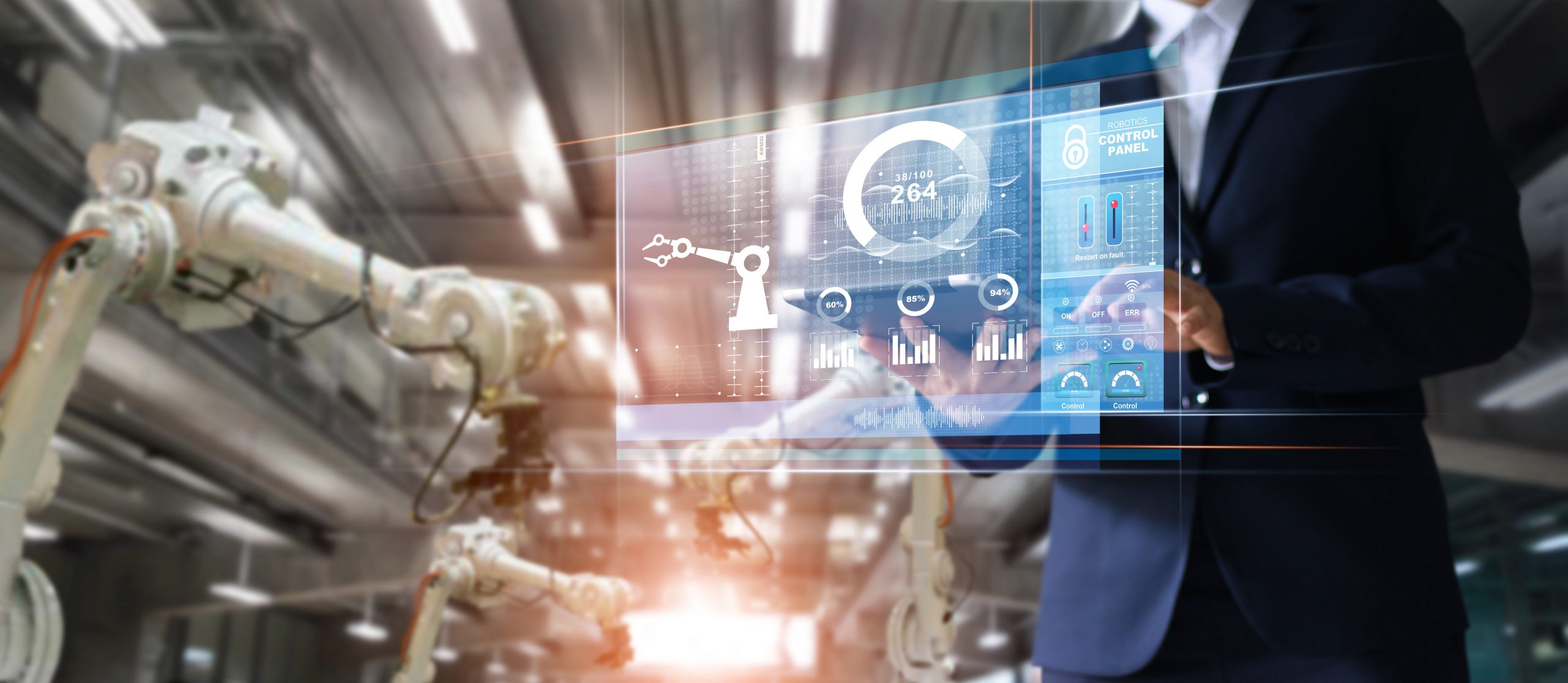
Scalable HMIs
Adaptation of materials with surfaces that are sensitive to pressure and deformation in order to set up feedback and thus control systems remotely.
Its HMIs are scalable, adaptable to all surfaces, multi-touch, etc. – Each material can become an HMI!
Our sectors
Aeronautics/Space
Touch Sensity is used for the detection of impact on fuselage, the non-destructive testing of composite parts, the characterisation of peeling and fibre breakage damage, and much more.
Our sectors
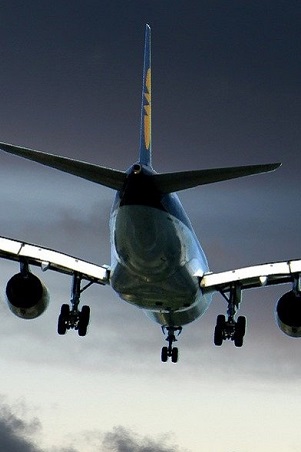
Aeronautics/Space
Touch Sensity is used for the detection of impact on fuselage, the non-destructive testing of composite parts, the characterisation of peeling and fibre breakage damage, and much more.
Nos secteurs
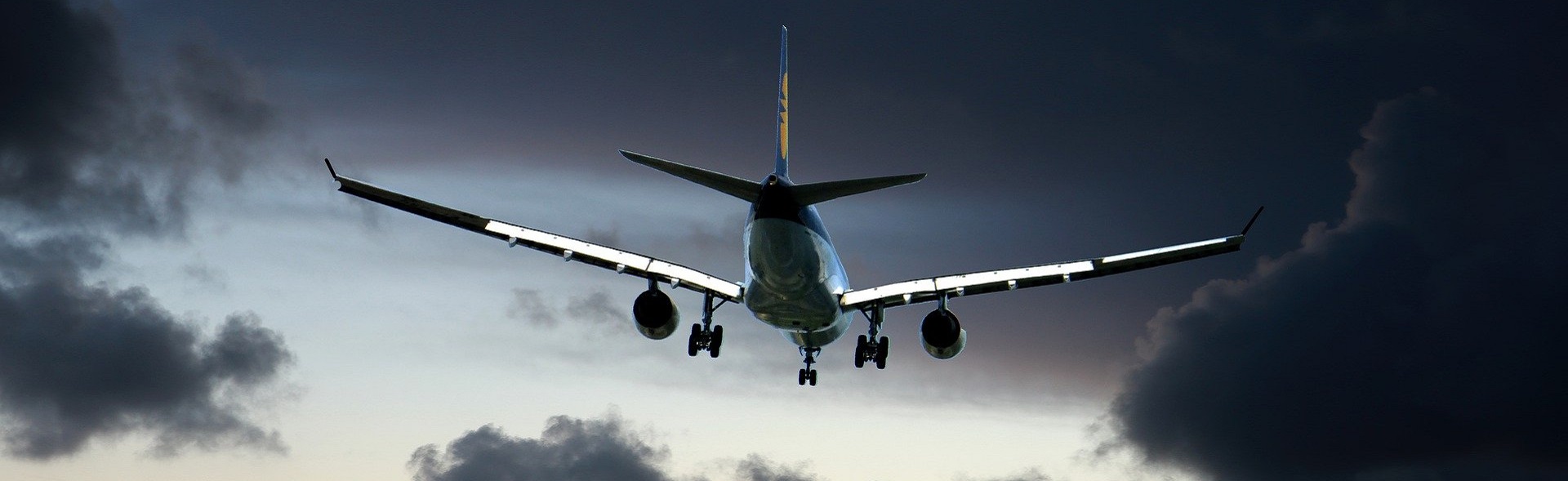
Aéronautique/Spatial
Touch Sensity intervient dans la détection d’impact sur fuselage, dans le contrôle non destructif de pièce en composite, dans la caractérisation des endommagements de type délaminage et rupture de fibre et bien d’autre.
Transportation
Thanks to the Sensity Tech technology, many use cases are now feasible, e.g. detection of impact on bodywork, the assessment of damage on structural parts of trains or tactile dashboards.
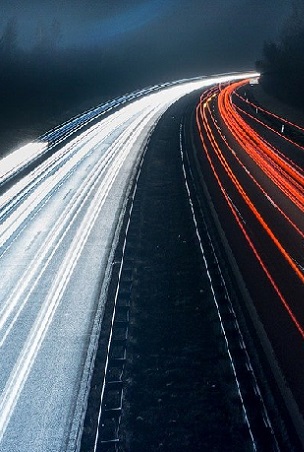
Transportation
Thanks to the Sensity Tech technology, many use cases are now feasible, e.g. detection of impact on bodywork, the assessment of damage on structural parts of trains or tactile dashboards.
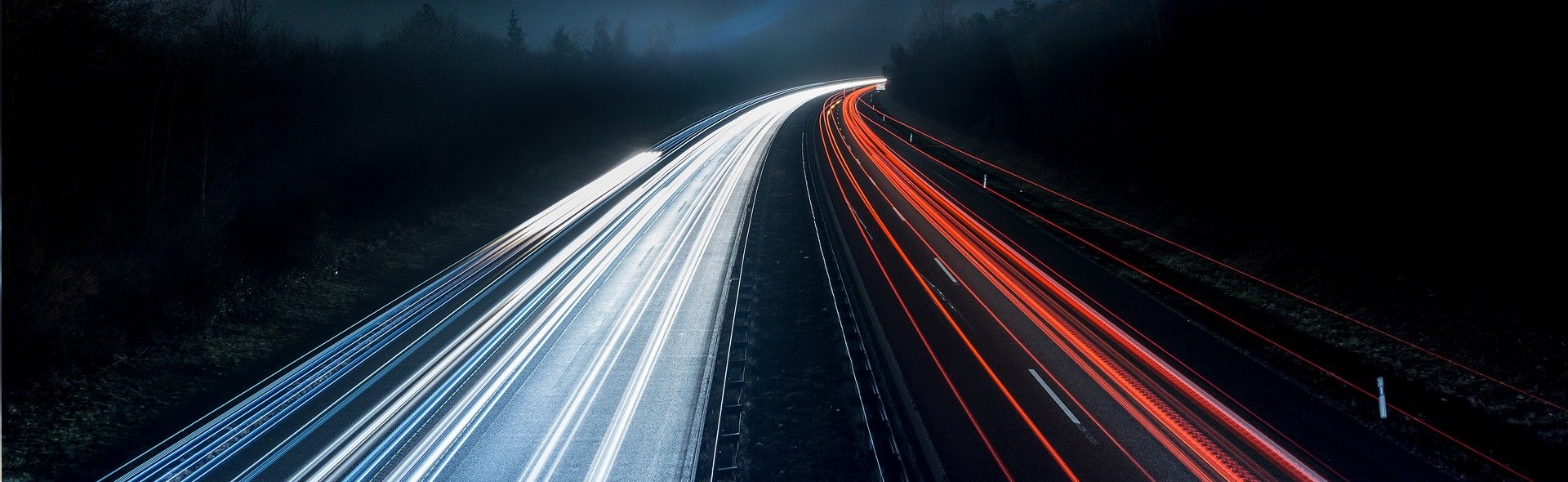
Transportation
Thanks to the Sensity Tech technology, many use cases are now feasible, e.g. detection of impact on bodywork, the assessment of damage on structural parts of trains or tactile dashboards.
Industry
Non-destructive testing in production lines, adaptable HMI, connected floor for safety; Sensity Tech can meet a wide range of needs in both building management and process automation.
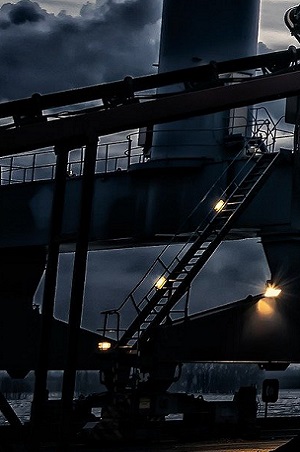
Industry
Non-destructive testing in production lines, adaptable HMI, connected floor for safety; Sensity Tech can meet a wide range of needs in both building management and process automation.
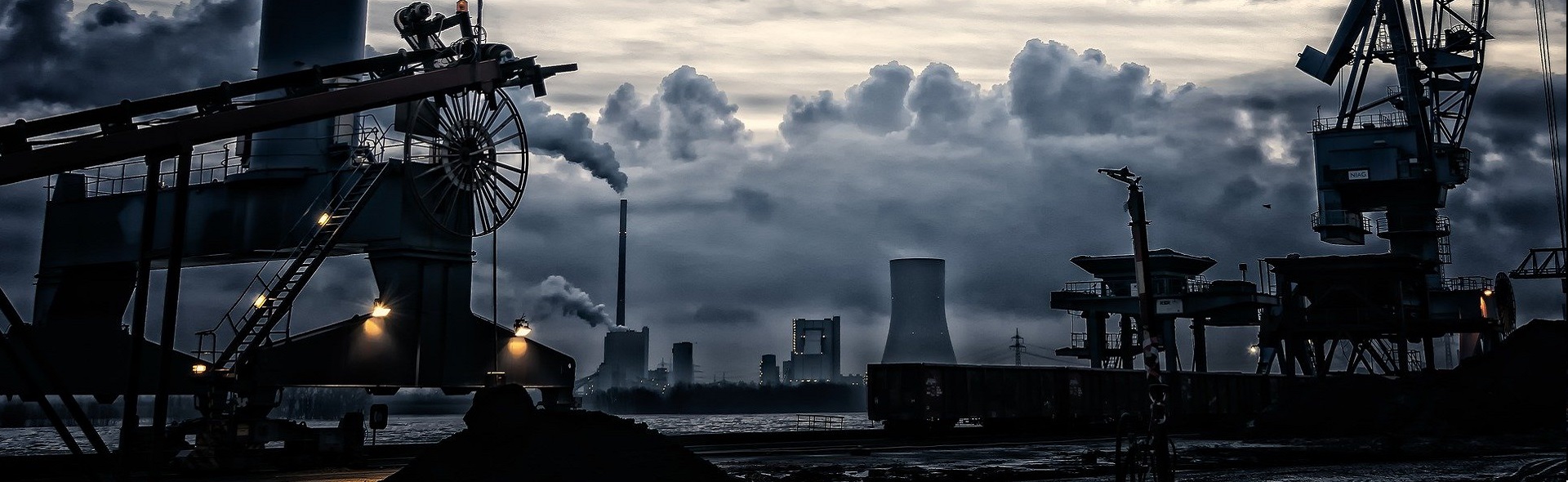
Industry
Non-destructive testing in production lines, adaptable HMI, connected floor for safety; Sensity Tech can meet a wide range of needs in both building management and process automation.
Defence
With its innovative solution, Touch Sensity steps up to meet the challenges of not only material health and structure monitoring for land vehicles, ships and aircraft, but also in the evolution of equipment for the soldier of the future, and the security of buildings and areas.
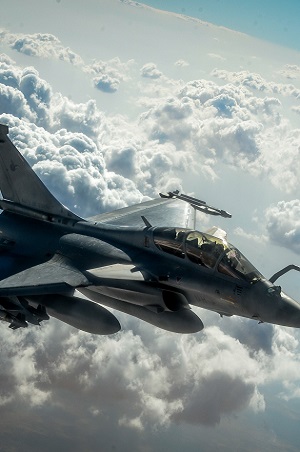
Defence
With its innovative solution, Touch Sensity steps up to meet the challenges of not only material health and structure monitoring for land vehicles, ships and aircraft, but also in the evolution of equipment for the soldier of the future, and the security of buildings and areas.
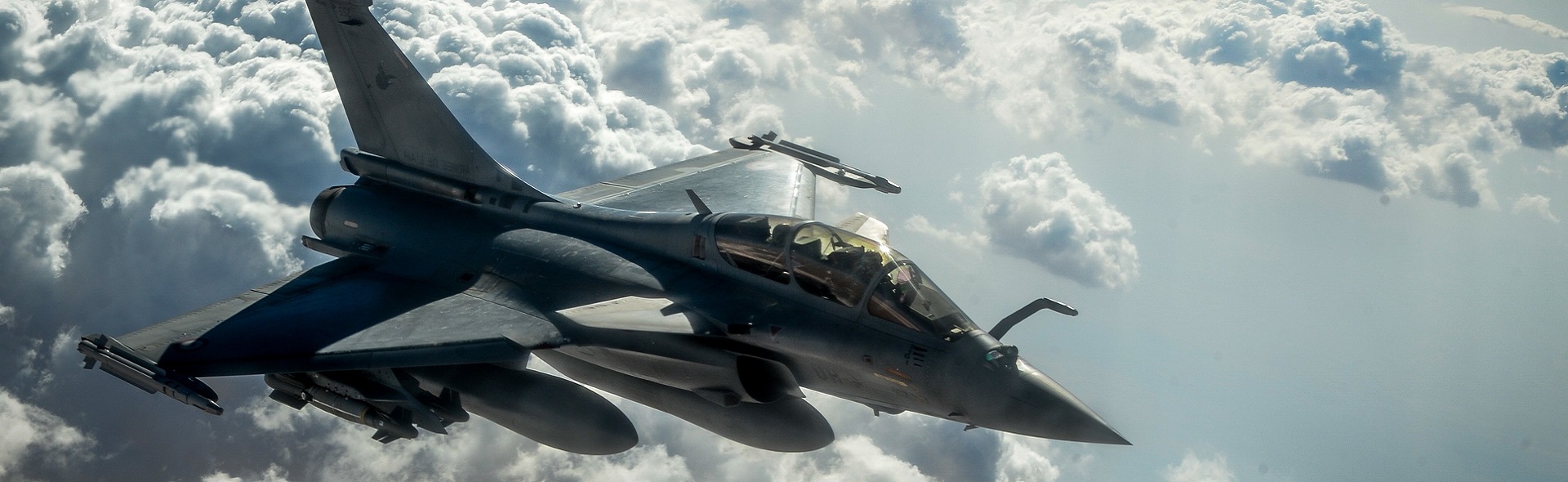
Defence
With its innovative solution, Touch Sensity steps up to meet the challenges of not only material health and structure monitoring for land vehicles, ships and aircraft, but also in the evolution of equipment for the soldier of the future, and the security of buildings and areas.